IN-W300
项目背景
某机械制造公司业务范围包括两轮车动力系统、三轮车动力系统、四轮车动力系统、通用动力机械、农用动力机械,并逐步构建柴油和电驱动动力的能力,为客户提供动力匹配的一体化解决方案。
大量数控设备的增加给企业生产带来了积极变化,生产柔性提高、生产效率提高、产品质量提升,为企业创造了可观的效益。但随着生产任务的快速增长,以及公司这种多品种、大批量的生产模式等情况,机加部在生产管理方面面的压力越来越大。
在引入制造物联系统前,企业数控车间的生产管理基本上采用传统的“半系统+人工+纸质”的工作模式,虽然形成了一套工作体系,但还是存在人工传递信息缓慢、各种信息反馈及处理效率低下、大量数量无法收集及统计分析等一系列问题。而生产前的准备工作主要通过车间与外部门电话、口头、派出人员等方式获取资料,以及在车间内部通过打印单据、人工传递、手工填写表格等方式进行流转,这种传统的作业管理方式严重制约着生产效率的进一步提升。
面对数控车间管理的种种不足,该企业迫切的希望建立数控车间协同工作的信息化平台,建立数控车间生产现场实时信息监测采集平台,实现实时故障信息的实时反馈、实时监控,从而有效提高生产现场故障处理的效率,提高故障处理过程的透明度。
方案简介
在该企业引用的制造物联系统中,产品与车间关键资源(设备、人员、物料)进行集成,以无线传输的方式搭建集团内部的物联网平台:
1. 直接从加工设备上采集实际工艺参数、生产节拍,防止数据的失真,减少由人工统计的误差和延迟导致的决策延误;
2. 详细的现场数字化信息(时间、设备、人员、批次等)为生产的实时监控提供了基础的数据来源;
3.对于设备停机状态和管理应答等有不确定性的数据,使用采集器上的键盘进行输入,弥补了自动数据采集的不足;
4.避开设备自动控制系统的协议限制,实现所有加工设备的联网和生产全流程控制;
5.不改变现有生产布局、装备水平和管理能力的情况下,实现精益和敏捷生产;
6.减少人工派工、人工输入、减少纸张的使用;
7. 直接在终端处上报停机信息,并发送短信至相关责任人,引导生产主管和生产支持职能部门快速处理生产异常。采集的生产现场数据的准确性和及时性,可以一方管理人员可以快速了解车间的实时生产情况,操作同时可以通过业务终端实时请求管理人员进行支持;
8.工艺图纸的电子化管理、操作第一时间了解工艺图纸适时调整生产;
9.设备维修详细记录,清楚了解现有设备的情况,通过加工程序管理将加工程序、数控设备、生产工单进行绑定,加工程序管理透明化。
系统架构
业务价值
通过系统产品进行生产车间的关键资源数据联网的构建、生产任务的计划分配,采集并管理生产过程中的各种设备与加工信息,为企业提供车间现场的各种数据,以方便企业对车间生产任务及时进行调整,提高了企业的生产效率,提升了企业的产品品质。
产品介绍
IN-W300智能业务终端 多达6种数据采集格式
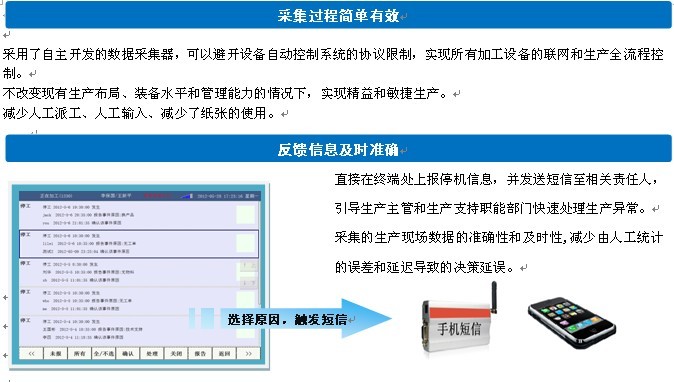 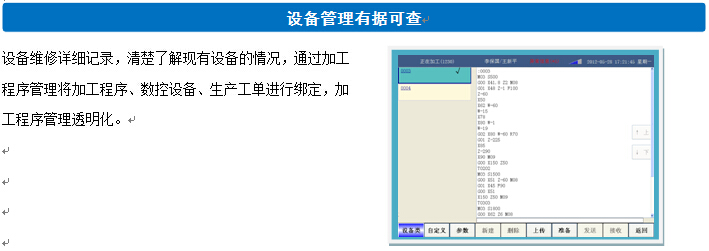 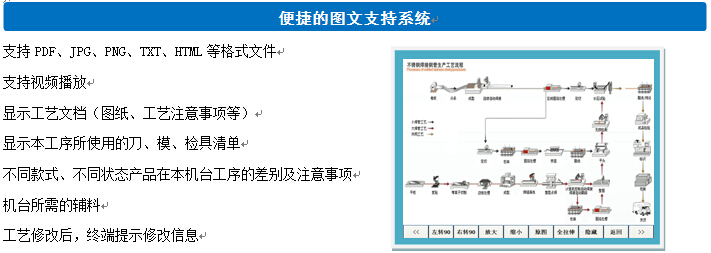
产品基本规格
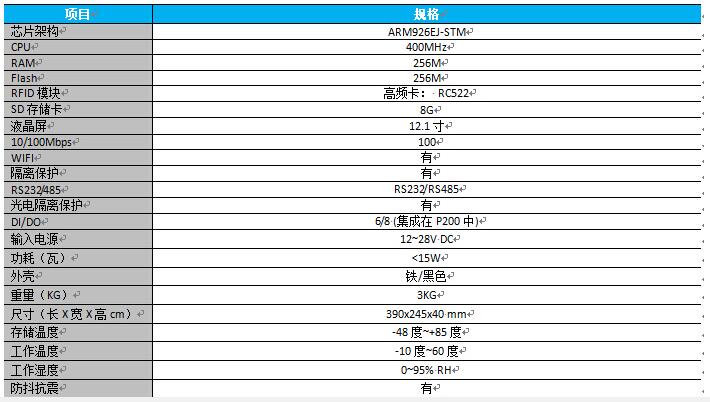
|